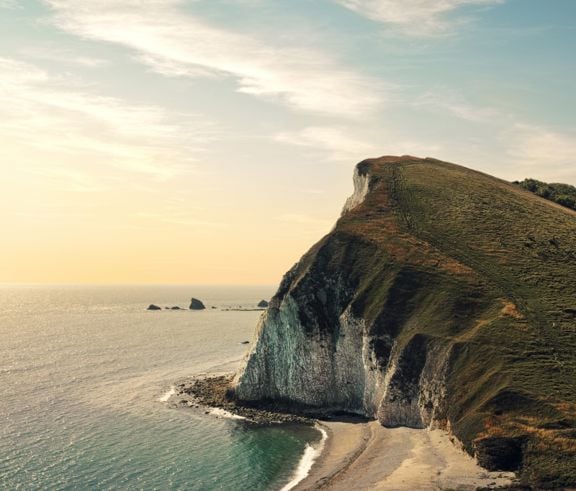
Page not found
The page you requested cannot be found. Please make sure that the address is spelled and formatted correctly. The page might also have been moved or deleted.
The page you requested cannot be found. Please make sure that the address is spelled and formatted correctly. The page might also have been moved or deleted.